Шнеки
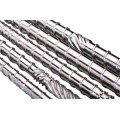
ЗДОРОВЬЕ ВАШЕГО ЭКСТРУЗИОННОГО СЕРДЦА
или когда пора менять шнек
- От чего умер больной?
- От гриппа.
- А-а... Hу, это не страшно.
Вопрос, который вынесен в заголовок, волнует каждого переработчика пластмасс, применяющего шнековые экструдеры. Оценить износ шнека достаточно трудно. Еще труднее бывает определить потери, связанные с изменением геометрии шнековой пары. А потери эти, между прочим, могут быть сопоставимы с прибылью предприятия.
Для того чтобы понять причину убытков, связанных с ухудшением параметров экструдера, необходимо разобраться в некоторых тонкостях его работы. Для начала давайте взглянем на фрагмент чертежа реального шнека номинальным диаметром 45 мм.
Обратите внимание на две цифры, +0,05 и -0,10. Это допуск на отклонение диаметра шнека. Это значит, что шнек должен иметь диаметр в каждом сечении от 44.90 до 45.05 миллиметров. Уложиться в такой «космический» класс точности очень непросто. К тому же это просто «дорогое удовольствие». Возникает закономерный вопрос: «А зачем?»
С большим значением допуска все вроде бы понятно - если увеличить диаметр, то шнек просто не влезет в гильзу материального цилиндра. Но зачем нужно загонять производителя в жесткие минусовые «пять соток на сторону»? Это всего-то 0,1% от диаметра.
Ответ, на первый взгляд, прост. Глубина нарезки шнека – всего два миллиметра. По отношению к высоте гребешка пять соток уже составляют 2.5%. Напрашивается простой вывод о том, что производительность шнекового экструзионного пресса уменьшиться в связи с этим на такую же величину. И это будет ошибочное суждение!
Большинство экструзионщиков искренне верят, что давление в шнеке создается по всей длине за счет «соскребания» расплавленного полимера спиральным гребешком с внутренней поверхности гильзы. Однако это не так. К примеру, аналогичные по конструкции шнековые насосы для перекачки вязких жидкостей редко преодолевают планку давления в десять атмосфер. Там, кстати, нет таких высоких требований к точности изготовления. Так что напорно-расходные характеристики от зазоров зависят мало.
Посмотрите на полученный экспериментальным путем график изменения давления по длине шнека. Это данные Штутгардского университета.
Верхний график соответствует классическому шнеку, который установлен в большинстве экструдеров. Многие специалисты знают, что давление создается полимерной гайкой на первых витках шнека. При этом оно достигает значений сотен атмосфер. Дальше оно не только не растет, но, наоборот, чаще всего падает. То есть вместо спирали могли бы быть любые другие смешивающие элементы. Кстати, известны шнеки с каналами, представляющими собой обратные спирали или узкие щели. И ничего, работают!
Но вернемся к потере производительности из-за зазора между шнеком и цилиндром. Реология, как известно, наука о парадоксальном поведении жидкостей и потому житейский опыт чаще вредит, чем помогает найти правильные ответы. Так и в данном случае. Дело в том, что по известным формулам, при уменьшении сечения вдвое его сопротивление движению расплавленного полимера растет на 3..4 порядка. То есть утечки через зазор в 2.5%, согласно теории, составят ничтожные доли процента. Так в чем же дело?
Пионерами в области переработки полимеров были, увы, не мы. Так что обратимся еще раз к зарубежному опыту. Специалисты НПО Пластик на рубеже 80-х и 90-х годов активно сотрудничали с представителями фирмы Райфенхойзер. Это немецкое предприятие многие считают лидером в области экструзии. На вопрос, что происходит при увеличении зазора, немцы отвечали, что снижается качество проработки расплава. Описание механизма этого явления в открытых источниках, несмотря на их обилие, нашим сотрудникам найти не удалось. Тем не менее хотелось бы обратить внимание на некоторые важные обстоятельства, способствующие «плохому поведению» изношенного шнека.
Давайте еще раз взглянем на график изменения давления по длине. Падение давления достигает десятков атмосфер на одном витке. Ранее тут уже говорилось о низких напорных способностях шнековых насосов. То есть, чтобы получить такие перепады, полимерный материал должен иметь очень высокую вязкость. К этому мы еще вернемся. С другой стороны, вязкость полимеров снижается на порядки даже в рабочем диапазоне сдвиговых нагрузок (от десятков до пары сотен килопаскаль). А где сдвиг достигает самых больших значений? Правильно – в узких зазорах между движущимися частями шнека.
Исходя из сказанного можно предположить, что, как только давление в районе движущейся полимерной гайки достигает сотен атмосфер, на поверхности ее трения о металл происходит интенсивное образование сильно разогретой высоко-текучей фазы полимера, которая устремляется в сторону пониженного давления. То есть вперед по ходу шнека. Двигаться в этом направлении она может по одному из двух путей. Либо в «правильном» направлении, то есть по спиральному каналу. Либо сразу «на выход» по зазору между шнеком и цилиндром. При этом высокие напряжения сдвига в зазоре не только существенно снижают вязкость расплава, но и дополнительно разогревают его, способствуя росту вредных утечек по внутренней поверхности гильзы. При таком положении дел даже небольшие зазоры приведут к сепарации расплава на две фазы – «честную» холодную и перегретую «блатную». Косвенно это подтверждается быстрым падением давления в компрессионной зоне, куда, как снег в водосточную трубу, «упирается» холодный материал.
Мы проводим оценку градиента температур расплава по на выходе из шнекового пресса. Надо сказать, что расплавы полимеров при экструзии далеки от турбулентного режима и только при «жесткой» соэкструзии по границам слоев может происходить нарушение этого правила. То есть обычно разные по вязкости фазы расплава полимера движутся ламинарно и не при этом смешиваются. Менее вязкая часть потока при этом будет обволакивать, согласно принципу совместного движения разновязких сред, более холодную часть полимерного сырья. Это можно определить по более высокой температуре пристеночных слоев. У хорошего пресса разброс температур не должен превышать 20 градусов, что тоже, конечно, многовато. Можно представить, насколько хуже показатель у плохих или изношенных шнеков. Чем это плохо?
Чтобы получить высококачественные полимерные материалы, будь то профиль, пленка или, скажем, мастербатч, необходимо обеспечить хорошее перемешивание полимерной массы. Особо плохой промес иногда заметен в виде разводов красителя. Обычно же недостаточную гомогенизации расплава определить трудно.
Плохо проработанный расплав приводит к ухудшению однородности продукции, увеличению расхода сырья из-за отклонения геометрии изделий от заданных значений, к росту отходов и брака из-за увеличения продолжительности выхода на заданные режимы. Кроме того, растет удельное потребление энергии, а перегретый материал требует дополнительного охлаждения, что может также снижать производительность оборудования. Отдельных исследований заслуживает влияние увеличенных зазоров в шнековой паре на термическую и механическую деструкцию полимера.
Кстати говоря, расплав с неравномерным полем температур и вязкости на выходе из шнека можно догреть и домешать только в статических смесителях, но там возникают другие проблемы.
Все указанные факторы приводят к серьезным потерям, которые переработчики не замечают только потому, что изменения к худшему происходят постепенно. В этом смысле ситуация с нарастанием потерь напоминает анекдот, вынесенный в эпиграф. Мы на практике часто сталкиваемся с тем, что заказчики обращаются к нам с вопросом о замене шнека только тогда, когда производительность экструдера падает вдвое по сравнению с номиналом. Порядок потерь при этом может достигать, в зависимости от конкретной ситуации, от 5 до 10 процентов стоимости перерабатываемого сырья и в десятки и даже сотни раз превышает стоимость замены шнека. Шнек – расходный материал, а скупой платит дважды.
А все-таки, как часто надо менять шнек?
Мы рекомендуем снимать шнек для оценки износа через первую тысячу часов работы и далее через 5000 часов (примерно раз в год). Если шнек качественный, то его износ зависит наличия абразивных частиц размером более 10 мкм. Даже при идеальных условиях износ происходит в связи с неизбежным попаданием пыли в сырье. Оптимальный срок замены высококачественного шнека при отсутствии «отягчающих факторов» составляет от 10 до 20 тысяч часов, что примерно соответствует 2..3 годам непрерывной работы. При этом внешне шнек может практически не отличаться от нового, но, как будет показана далее, это не означает, что его нужно использовать. Ускоряет износ, в порядке увеличения воздействия, использование высококачественной «вторички» (например, переработанной кромки), меловые наполнители со средней тонкостью до 10 мкм, отсутствие специальных мероприятий, направленных на снижение запыленности воздуха на производстве, а также некачественные добавки. Срок службы шнека также сокращается, причем уже в разы, при использовании привозной «вторички», диоксида титана и других абразивных добавок, работе с коррозионно-активными полимерами. Гильза при этом служит примерно в 5..7 раз дольше, но ее тоже рано или поздно нужно менять.
Хотелось бы еще раз отметить, что измерение износа – дело непростое. Для того нужна, как минимум, чугунная плита. Для выполнения замера лучше обратиться на ближайшее инструментальное производство. Подсказка: износ наиболее быстро идет в районе формирования полимерной гайки, то есть на расстоянии 4..5 диаметров от бункера.
Желаем успехов и процветания вашему делу!
Смышляев А.Р., ктн
НПО Арсенал